Electrical Conductivity in Vehicle Coolants
Any company that has been developing coolants for some time has developed the muscles required to pass the traditional ASTM tests that validate proper corrosion protection, stability, material compatibility, pH and freeze point (to name a few).
The coolant consumer can be assured the product they select has gone through the same stringent testing as every other product on the shelf.
This has undoubtedly led to consumers making purchasing decisions based upon brand loyalty or cost.
But new-energy vehicles are changing this in a few ways:
- New-energy vehicles have different metals to protect from corrosion.
- New-energy vehicles operate at different temperatures than traditional internal combustion engines.
- New-energy vehicles have batteries and other components at risk of electrical fire.
We have previously explored how to ensure protection of the different metals found in new-energy vehicles. This article will explore how and why original equipment manufacturers (OEMs) and consumers can select a coolant that can reduces safety risks associated with batteries and leaked coolants.
The secret is to understand electrical conductivity — not all electrical conductivity tests are created equal.
Electrical Conductivity of Coolants
Electrical conductivity measures the ability of a substance to conduct an electrical current. Substances high in electrical conductivity are better conductors of electrical currents than substances low in electrical conductivity. This is why copper, with a high electrical conductivity, is used in household appliances and common electrical equipment to pass currents.
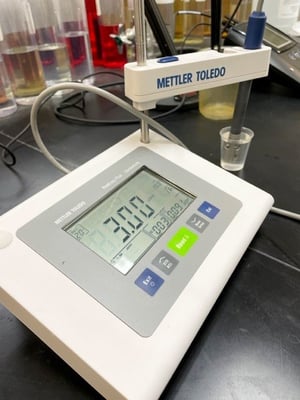
Electrical conductivity for coolants is measured in microsiemens per centimeter (µS/cm). A sample conductivity meter setup can be seen in the image to the right. The test probe is dipped into the coolant solution, after which the conductivity reading typically appears within seconds.
The electrical conductivity found in traditional internal combustion engines ranges from 3,000 µS/cm to 5,000 µS/cm. However, the electrical conductivity is irrelevant if your coolant is being used in an internal combustion engine because there are no batteries or associated components that would be at risk of fire if a coolant were to leak. Therefore, electrical conductivity had never been a specification for the internal combustion engine (nor had coolant manufacturers even thought to test).
However, if you are using a coolant in a new-energy vehicle, knowing a coolant’s electrical conductivity is not only relevant, but you will likely require an electrical conductivity that is a fraction of that found in current off-the-shelf coolants.
The time has come for coolant manufacturers to not only add “electrical conductivity” to their vocabulary but also to develop standard testing protocols for this specification.
Since there are not yet ASTM standards for new-energy vehicle coolants, we have noticed that not all electrical conductivity test results are created equal. (Update: In 2023, ASTM published new test standards for electric vehicle coolants.) Specifications vary by OEM.
We will now explore:
- The electrical conductivity requirements we are hearing from the industry
- How time and temperature impact electrical conductivity results
Coolant Electrical Conductivity Requirements for New-Energy Vehicles
If there's one thing for certain, it’s that the electrical conductivity range of 3,000 µS/cm to 5,000 µS/cm will be too high for most, if not all, new-energy vehicles.
Most electric vehicles on the road today are using standard off-the-shelf organic acid technology (OAT) coolants that were manufactured for the internal combustion engine. The main reasons are: 1) there were no EV coolants on the market then and 2) there were no specifications requiring lower electrical conductivity.
Over the past 12 months or so, both conditions have changed.
What we have found is that although there is a range for the specifications our new-energy vehicle partners have requested, they tend to cluster around similar numbers depending on if they are an electric vehicle or a fuel-cell vehicle manufacturer:
- On the higher end of the spec, electric vehicle manufacturers are requesting <100.0 µS/cm to reduce the risk of electrical fires in the event of a coolant leak.
- On the lower end of the range, fuel-cell vehicle manufacturers have the longevity of their fuel-cell filters in mind when they request <3 µS/cm. This is a broad range that has major implications on the technological breakthroughs that would have to occur in a coolant R&D lab.
So, although this isn’t an ASTM standard yet, the electrical conductivity for new-energy vehicles ranges from 3.0 µS/cm to 100.0 µS/cm. This requirement is just a fraction of the electrical conductivity found in current non-EV/FC coolants. The coolant industry needed to make technological leaps to meet that requirement for new-energy vehicles.
We have been in the coolant industry for a long time. It’s no surprise to us that when the industry was asked to leap, the industry said how high. There are now a few electric vehicle and fuel-cell vehicle coolants that meet these specifications. Each of the companies that made the necessary technological breakthroughs has delivered a product better suited for new-energy vehicles than your grandfather’s coolant.
However, the lack of ASTM testing protocols has exposed some variation in how electrical conductivity is reported.
Measuring Coolant Electrical Conductivity Over Time and Temperature
We have already explored how straightforward it is to test for electrical conductivity. However, since a new-energy vehicle is intended to move, it will create heat. Therefore, evaluating if a coolant meets electrical conductivity specifications is not quite this straightforward.
We must evaluate the coolant over both time and temperature.
Five coolant samples were chosen which are currently being used in EV indirect cooling. These are coded as:
- D1 EG Premix50/50
- G1 EG Premix50/50
- J1 EG Premix50/50
- V1 EG Premix50/50
- D2 EG Premix50/50
An experimental setup of a Parr reactor test is shown in the image below.
The test conditions used are as below:
- Temperature: 150°C (302°F)
- Pre-charge of air: 90 PSI
- 10 feet copper wire
- Duration: 2 weeks
- Sample withdrawal intervals: 7,14, and 20 days
- Measurement parameters: pH, conductivity, and color change
These parameters were considered since earlier [1] authors from Dober and Cummins Fleetguard developed this method to model primarily the thermal stability of heavy-duty coolants in 300,000-400,000 miles of actual service.
Testing Takeaways
Figure 1 and figure 2 below show electrical conductivity and pH data of all five samples. In the indirect cooling applications where water-based fluids with corrosion inhibitors are generally used, the electrical conductivity of the liquid coolant mainly depends on the ion concentration in the fluid stream. The higher the ionic concentration, the higher the electrical conductivity of the fluid.
The increase in ion concentration in a closed-loop fluid stream may occur due to ion leaching from metals and nonmetal components with which the coolant fluid is in contact. During operation, electrical conductivity of the fluid may increase to a level that could be harmful for the cooling system.
Figure 1: Percent change in conductivity
Figure 2: Percent change in pH
The electrical conductivity of J1 starts increasing immediately during the start of the Parr reactor. By the end of 450 hours, it attains the highest percent change in conductivity (450%).
Under the same test conditions, D1 and other coolants' electrical conductivity remain below 25%. It is interesting to note that the initial pH of J1 is lower than all other coolants. However, after 482 hours it has the highest drop in pH.
The Parr reactor experiment clearly indicates that ion leaching of both metals contributes to an increase in the electrical conductivity of the coolant fluid.
On the other hand, G1 has the lowest drop in pH and lowest rise in electrical conductivity. It can be hypothesized that there exists some correlation between pH and stability of electrical conductivity besides the individual robust corrosion package quantity and quality used in these formulations.
These results are striking because formula J1 had both the lowest initial electrical conductivity and the lowest initial pH.
In short, you should be careful to select a coolant based upon initial electrical conductivity without testing over time and temperature.
REFERENCES:
1. Yu-Sen Chen et al., Comparison of bench test methods to evaluate heavy duty coolant thermal stability, Journal of Testing and Evaluation, May 2006, ASTM