Dober's Innovative Super Syrups Reduce Costs for Blenders
Blenders around the world struggle to blend cost-effective coolants with the quality and performance expected of world-class suppliers. The problem becomes more glaring as marketing and distribution of coolants become global.
Challenges of Coolant Blending ‘From Scratch’
Traditional coolant technology involves mixing discrete anticorrosion chemical components in a blending tank. There may be as many as 15 different chemicals in a typical coolant formula. This process takes up to 12 hours to complete, as some powdered chemicals take a long time to dissolve.
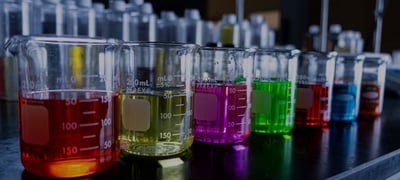
For blenders, the extended time to blend means the tank is occupied and other blending cannot take place, representing foregone revenue.
Additional costs are incurred with the “from scratch” blending method, which include purchasing of discrete chemical components, inventory of the components and regulatory costs to manage dangerous powders.
In addition, this blending procedure is complicated and results in inconsistencies and mistakes, especially bringing on new toll blenders internationally.
Dober’s Super Syrup Offers Easy-to-Follow Blending Procedures
Dober’s innovative Super Syrup formulation technique involves blending the necessary formula ingredients into a super-concentrated water-based syrup. Only a very small amount of Super Syrup is needed (typically 1-5%).
Dober provides easy-to-follow blending procedures that allow consistent quality blending in a minimum amount of time (as short as 30 minutes).
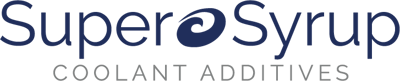
These are not easy formulations to develop, but creating sophisticated one-component systems is a high priority in Dober’s advanced R&D laboratory.
The methods are so difficult that patents are applied for in select cases, not because of the corrosion chemistry but because the one-component formulation is difficult to achieve with stability while allowing for global coolant blending at minimum cost.
Super Syrup Eases Supply Chain Strains, Reduces Costs
For global supply chains, this model is imperative.
Coolant suppliers that have international business typically export coolant concentrate (the coolant without water).
Even without water, freight costs to ship glycols and additives are extremely high compared to the Dober model. Lead times are extremely long and working capital is tied up on the water for weeks.
Developing a supply chain network to blend super syrups locally creates high value to global companies that want to remain competitive with local coolant suppliers.
Learn About our Global Supply Chain >
Dober Difference in Coolant Technology
Dober understands complex additive blending and has trained select global blenders how to blend complex formulations.
We now offer blending on four continents to meet the needs of global coolant suppliers. In turn, they can lower costs and lead times, in addition to gaining a competitive advantage over companies that follow the old traditional “from scratch” and exporting finished concentrate model.
In addition, we have developed global sourcing expertise. Our global blending network can access local supply of quality corrosion inhibitors, further lowering cost and creating utmost efficiencies. This also allows broad sourcing security — in case sources in one region are disrupted, other regional sources can be accessed.
Innovation can materialize in different ways. Dober pursues corrosion technology innovation to develop sophisticated coolant additives for tomorrow’s engine cooling systems. We also innovate with our supply chain strategy to lower costs for global coolant companies and create greater efficiencies for them to remain competitive and to better service their end-user customers.
Interested in learning more about Dober's Super Syrups and how we can help your operation? Click below to learn more.