CIP Cleaning Optimization
Introduction to CIP Cleaning Optimization
CIP, or Clean In Place, is a system of automated cleaning without the need for dismantling the equipment. It utilizes the Time, Action, Chemistry, and Temperature (TACT) parameters for effectively cleaning. This article will explore:
- Considerations for a New CIP System
- CIP Cleaning Chemical Attributes
- Optimizing your CIP Process
10 Considerations for a New CIP System
A CIP system is often confused with a Wash in Place system. The major difference between the two is the level of automation. A general industry understanding is that CIP systems are completely automated and have defined cleaning programs that could be set with variably adjustable temperatures, dosage, and time. Any system with a lower level of automation but not requiring dismantling of the equipment is WIP.

Before finalizing a new CIP system, the following points need to be considered to ensure flexibility needed for automated cleaning of a wide range of excipients with appropriate cleaning chemicals.
- Cleaning goals vs. space and utilities: Are either space and utilities a constraint to achieve your goal faster? Depending on the answer, you could consider a portable CIP system, single tank design, or stationary two-tank system with a separate solution and rinse tank.
- Complete coverage in minimum time: Based on the Riboflavin test, the minimum time and volume of solution required to reach all parts of the equipment could be determined. For faster cleaning, it is better to have multiple spray devices at different locations to cover the entire area effectively. The spray devices (whether to use static or dynamic spray balls) could be decided based on the equipment design, coverage, and cost.
- Pressure: Impingement is important for efficient residue removal. Spray balls delivering the cleaning solution at low pressure due to the CIP design leads to soaking of the residue which would take a longer time to dissolve/disintegrate and go into solution when compared to high-pressure impingement that gives better cleaning action
- Flow: Turbulent flow is critical to provide the mechanical action necessary for the removal of soils. Fluid velocity of 5 ft/sec is the minimum recommended velocity to achieve turbulent flow of aqueous solutions in piping systems. Based on the equipment design, the adequate flow should be determined, and the CIP system design should conform to it.
- Recirculation & Reheating: An ideal CIP system must have a recirculation system that will
- enable reheating of the cleaning solution to maintain detergent temperatures, cleaning efficiency and avoid excessive foaming due to detergent temperature drop
- utilize minimum detergent quantity as compared to ‘straight to drain’ option
- enable continuous impingement action through spray devices which a ‘holding and soaking’ system is unable to do
- Adjustable variables (temperatures, flow, detergent dosing): A flexible system is advantageous for a long-term requirement. It may not be required for the current products, detergent, or cleaning procedure, but with continuous innovation and newer excipients, the CIP should be able to modify cleaning cycles as per requirement
- Drainage: It is important to drain the rinses as well as the detergent solution with residue in the most efficient manner to avoid deposition around the drain. Also, the system should be designed in a manner that allows fast drainage to enable quick transition to the next step before the equipment surface dries. Drain utilities must be capable of handling high discharge temperatures equal to CIP temperatures unless cooled by additional utilities. Additionally, flow rates at the drain will be similar to the highest CIP circuit flow rate and the system should be able to handle it. If the system offers flexibility to collect or divert the discharge into a tank before disposal, it would be helpful in cases where the components need to be separated or neutralized as per EHS requirements.
- Ease of cleanability of the CIP system itself: During the cleaning process, the CIP tanks and pipes see a lot of excipients and detergents. For non-dedicated pharmaceutical equipment or portable CIP systems, it is important that the CIP system is easy to clean to avoid cross-contamination or microbial growth due to hidden residues.
- Ease of monitoring variables: It should be easy to monitor the set variables and calibrate the measuring instruments to ensure that the set process is followed.
- Cost: With the increase in flexibility, functionality, and automation, the cost of a CIP system naturally will increase. The best practice is to install an integrated CIP system with your equipment, which is more cost-effective than installing CIP system in your existing equipment. You must weigh your requirement versus the cost and take your decision accordingly considering the long-term return on investment.
Selecting CIP Cleaning Chemicals for Your System
Although Clean In Place Systems have been available for the food, personal care, and pharmaceutical industry for more than half a century, not all companies have them installed in spite of the listed advantages. A major reason could be that companies are hesitant to invest in such expensive systems when they have products that are historically known to be difficult to clean without manual scrubbing and intervention. The answer to this is to find the right detergent for the residues of the product processed in machines.
5 Attributes of a Good CIP Cleaning Chemical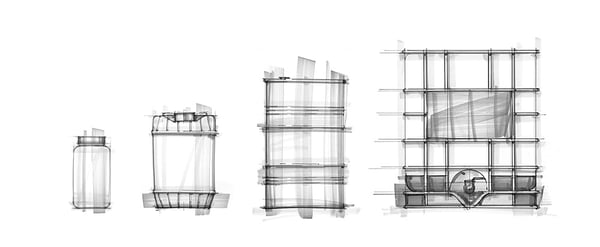
- It dissolves or breaks down the entire residue and keeps it suspended or in solution until it is drained off.
- The residue or soil should not come out as flakes or large sheets as these residue fragments could potentially clog pores, block the re-circulation pipes and reside in hard-to-reach areas, thus increasing the possibility of microbial or cross-contamination.
- Most of the pharmaceutical residues belong to formulations with multiple excipients. Targeting one excipient alone is not the right strategy as this could lead to multiple CIP cleaning cycles, increase in cleaning times, and water consumption. An effective detergent should be able to remove the entire formulation that could contain tough to clean pigments such as Titanium dioxide and Iron oxides.
- Even after the removal of residue from the equipment walls, the detergent solution must keep it dissolved or suspended, without which, the residue could re-deposit on different parts of the equipment or the CIP skid system and lead to product contamination.
- It works in low dilution (>10%) based on your CIP system’s dosing capacity, unlike in manual cleaning, which has the option of application, soaking and scrubbing with concentrated detergent, or possibility of addition mid-cleaning in WIP cleaning process
- It is easily rinsible and the set post-rinse procedure is able to repeatedly remove the detergent and residue traces
- It is low-foaming or has a defined temperature range for no foaming as foam could cause complications in the cleaning process and leave behind residue and stains
- It should be non-corrosive to the equipment as well as CIP skid contact MOC (material of construction)
Optimizing Your CIP Cleaning Process
There are a lot of guidelines for the QBD approach to develop any procedure, including cleaning. Similarly, the individual regulatory authorities have stringent guidelines for validation.
Ideally, companies would prefer using only water or at the most, a single detergent to clean their entire product portfolio. However, we all know and would agree that there are a group of products that need different detergent chemistries
Here are 5 steps that could be followed to develop an efficient cleaning procedure
- Confirm if the current cleaning detergent and procedure is suitable for the soil/residue in question by lab studies (for a new product) and historical data evaluation (for existing commercially manufactured products)
- In case the answer to the first question is a no, a Lab scale evaluation has to be performed with the recommended detergent(s) to determine the right cleaner and range of cleaning parameters. This could be done by replicating the soiling procedure on coupons (made of MOC comparative to the equipment) and performing cleaning studies representative to your CIP system.
- Scaleup considerations: Once the most effective detergent is confirmed, the possible variables during scale-up from coupons to actual equipment must be listed down to be assessed
- CIP capabilities (temperature, pressure, minimum cycle time based on coverage studies)
- Residue thickness based on maximum campaign size
- Maximum dirty hold time
- Minimum volume of detergent required for worst case scenario (b. & c.)
- Total surface area for scaling up the soaking/impingement time
- Scale-up trials and optimization study is the next step. The scale-up trials must be planned based on the scale-up consideration to develop the most efficient cleaning process in the worst-case soiling with minimum detergent concentration at optimum temperature conditions in order to increase your savings in all possible manner. In order to perform these trials in a commercial product machine, you must first ensure that you have a validated analytical method to prove the removal of the detergent from the equipment surface after cleaning and perform testing before manufacturing the next product or batches.
- Once you are satisfied with the optimized cleaning process and are convinced that it is robust, cleaning validation can be initiated.