Due to water’s high heat capacity and ability to evaporate naturally, it is the most efficient conduit of energy transfer and has many unique advantages when used in cooling processes, such as: cooling towers, chillers, plate and frame heat exchangers, shell and tube heat exchangers, and many more.
In fact, water has been used in mechanical cooling processes starting as early as the 18th century, when it was used to improve the efficiency of steam engines. Water has many advantages in the cooling process, but there are also potentially dangerous disadvantages, including corrosion, mineral scale, fouling and microbiological contamination.
These disadvantages can be managed and avoided with proper mechanical, operational and chemical treatment methods.
It is absolutely critical when managing water-based cooling equipment to not only be aware of these potentially destructive side effects but also know how to avoid and properly manage them. Proper management of a cooling tower, chiller, or other water-based cooling equipment can be broken down into three main components:
-
-
Mechanical – installing the proper equipment for your process and utilizing pretreatment greatly reduces the risk of breakdowns and unnecessary chemical requirements.
-
-
Operational – operating and maintaining your equipment to manufacturer recommended guidelines.
-
Chemical – the final component that is used to “polish” and improve system performance and should never be used in place of proper mechanical and operational measures.
Chemical treatment, while not the first line of defense, is critical to running a clean, efficient cooling system.
Mineral scale is chemically controlled via scale inhibitors such as phosphonates and dispersing polymers. Corrosion is chemically controlled via corrosion inhibitors such as azoles, ortho-phosphate, poly-phosphate and molybdate. Fouling is chemically controlled via dispersant polymers. In this edition of Cooling Water Treatment, we will discuss how to prevent and manage microbiological contamination by utilizing chemical biocides.
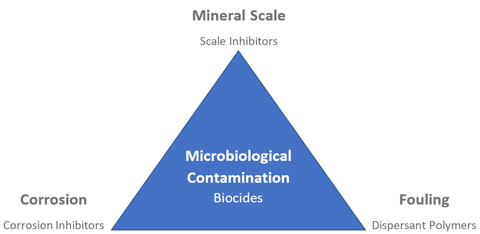
Like all living things, bacteria need food, water and the proper environment to live and grow.
Recirculating cooling systems provide water flow conditions and temperatures that increase the levels of oxygen, food and nutrients that bacteria need to thrive. Bacteria are introduced into the cooling water system from the air, the makeup water, or a process contamination.
There are two categories of bacteria: sessile (surface) and planktonic (bulk water).
Sessile, or attached bacteria, are more resilient to biocide treatment and can outnumber planktonic bacteria. Sessile bacteria can cause fouling and corrosion in a cooling system.
Planktonic, or free-floating bacteria, are more easily measured via the “dip-slide” method. The presence of both sessile and planktonic bacteria makes it all the more important to understand total system water volume and introduce complementary biocides dosed continuously at supplier-recommended levels.
Biofilms start as individual microorganisms that float in the water. When left untreated, they will migrate to an area where they attach themselves to a surface and begin multiplying. The biofilm continues to grow in surface area and mass, and migrates to form additional biofilm areas. When bacteria and biofilms form, they will attach to the metal and lead to metal degradation via corrosion, contamination and mechanical blockages – all of which result in reduced heat transfer, decreasing operational efficiencies.
In some cases, microbiological contamination can lead to the growth of a bacteria known as Legionella Pneumophila, which is the cause of Legionnaires' disease.
Prevent Microbiological Contamination with a Biocide Treatment Program
The ultimate objective of an effective biocide treatment program is to attack the microscopic organisms before they grow and migrate together, forming a biofilm.
The most common way to prevent nearly all forms of microbiological contamination in your cooling system is to utilize both an oxidizing and non-oxidizing biocide. Utilizing BOTH an oxidizing and non-oxidizing biocide is highly recommended because they attack bacteria in their own unique ways.
Oxidizing biocides are chemicals that have the ability to kill microorganisms through the electrochemical process of oxidation. An oxidizing agent, such as chlorine, pulls electrons in, while the bacteria it is attacking loses electrons. This loss of electrons causes the organism to die or, at least, prevents it from continuing its growth cycle.
There are many choices and mechanisms to control bacteria in cooling water systems. There are differences based upon how an oxidizing biocide is introduced into the water, how it will react with water, how it reacts with various compounds found in the water, their stability, their oxidizing power, their ability to penetrate biofilms, and their effectiveness.
Oxidizing biocides can be fed continuously or intermittently. Continuous feeding of an oxidizing biocide is always recommended for a system that has little to no existing microbiological contamination.
- If a continuous dose is fed and managed correctly it will require the least amount of maintenance and be the safest form of treatment.
- If a biocide is fed intermittently, it is critical that enough chemical is fed to kill the planktonic bacteria. However, be careful to avoid overfeeding, as this can be a safety risk and can potentially upset the other chemicals being fed.
Below is a chart summarizing some of the possible solutions, along with disadvantages, of each solution.
Non-Oxidizing Biocides
Non-oxidizing cooling tower biocides work through various exterminating processes such as interfering with reproduction, stopping respiration, or lysing of cell walls. Non-oxidizing biocides can be fed continuously to achieve a high enough concentration for a long enough period of time to kill the bacteria. A continuous feed of non-oxidizing biocide is recommended for small to medium size systems that are not experiencing severe microbiological contamination. Kill time can require several hours up to a day for systems with existing contamination.
Selection of a non-oxidizing biocide depends upon:
- Water pH
- Available retention time
- Efficacy against various bacteria, fungus and algae
- Biodegradability
- Toxicity
- Compatibility with the other chemistry
Non-oxidizing biocides are described below:
DBNPA (20% active)
2,2 Dibromo-3-nitrilopropionamide — DBNPA for short — has a short holding time as well as a fast kill rate.
The product breaks down into harmless byproducts that contribute to an increase in total organic carbon (TOC) levels (glycol-based TOC). DBNPA is also pH-dependent. A typical dosage of 100 ppm for 60 minutes is sufficient to control bacterial contamination. DBNPA can be deactivated by H2S coming from sulfate-reducing bacteria (SRBs).
Isothiazolin
Isothiazolin requires a longer contact time compared to DBNPA. Suggested dose rate is typically 100 ppm for 4 hours of contact time. Isothiazolin effectiveness is also pH-dependent. Isothiazolin is a very dangerous biocide, from a health perspective) and careful application of the product should be undertaken. Isothiazolin can also be deactivated by H2S coming from SRBs.
GlutAraldehyde
Glutaraldehyde requires long holding times (much longer than isothiazolin or DBNPA), as the kill rate is slow. Higher concentrations of product will lower the required contact time but increase treatment cost. Suggested dosage rates are 100 ppm of active glutaraldehyde for 6 hours. Glutaraldehyde can be deactivated by ammonia coming from denitrifying bacteria.
Quaternary Amines
Quaternary amines are similar to the above non-oxidizing biocides in effectiveness and applications are very system-dependent. The key problem with quaternary amines is due to their cationic (positive) charge. This positive charge will adversely react with anionic dispersant polymers, used for scale and corrosion management, resulting in product precipitation and reduced product effectiveness.
Every cooling system is different. There are many factors and safety considerations that must be considered when developing an effective microbiological control program.
A process of trial and error may be needed to find what works best for your system. Daily or weekly testing of your cooling process water will need to be done in order to ensure proper feed rates and control of microbiological growth.
For a free system analysis and biocide recommendations, reach out to talk with a Smart Release cooling tower expert.