Cleaning Pharma Equipment is Not Just One-Step in the Process
Equipment cleaning is often thought to be one step in the production process, however upon taking a closer look, it is an entire process to be developed and optimized on its own to maintain product quality and production output. There are many variables that impact equipment cleaning procedures for fluidized bed coaters, coating pans, and various blending equipment. This guide sheds light on cleaning procedure challenges for this equipment and how to address them.
Production is like a Beating Heart
So, who is this Guide for?
Manufacturing and Production is the beating heart of any pharmaceutical company. These critical teams are responsible for meeting often demanding market needs and adhering to strict regulations, all without compromising productivity and product quality. These tasks can often be demanding and overtly complicated to maintain, and the threat of an extended shutdown could mean loss of significant generated revenue. Having an incorrect cleaning procedure for any piece of pharmaceutical equipment can often be a root cause of these expensive shutdowns, specifically when it comes to the cleaning processes put into place for this equipment.
Cleaning Procedures are Not Created Equally
Every pharmaceutical cleaning procedure is unique and should be created based on the unique residues created and your cleaning capabilities. Without consideration of these variables:
- Incorrect cleaning procedures can cause manufacturing challenges - such as unnecessary use of excess resources.
- Optimal Cleaning is not taken into consideration during product development.
- Understanding capabilities of your equipment is the most important thing before cleaning.
- Different types of equipment pose unique challenges- you can't always expect one thing to work for everything.
Those Challenging Vertical Surfaces of Fluid Bed Coaters
Fluid bed coaters can be very large pieces of equipment that create their product by using a vertical spray coating and drying process. The cleaning process of a fluid bed dryer is largely determined by size of vessel, the residue needed to be cleaned, and the limitations of cleaning equipment. Because of the vertical surfaces, the most common challenge for a fluid bed is getting the detergent solution to stick to the vertical walls and/or to maintain contact of solution to walls. This can create the need for manual cleaning action. CIP cleaning, if available, should be considered as the consistent spray can help keep the vertical surfaces coated with detergent solution. Additional cleaning variables that should be looked at when developing this cleaning process are:
Facing an equipment cleaning challenge of your own?
Download this technical cleaning guide and discover how to address any challenge.
Tablet Coaters and Their Tough Coatings
Whether it's thick pooling of coatings or long dirty hold times in between batches... If these problems sound familiar, you are not alone.
Developing a cleaning process for a tablet coater, or coating pan, can be simpler than a fluid bed because of the smaller size and the ability to implement clean-in-place for additional action. The standard cleaning process for tablet coaters is to fill the tray with the detergent solution, soak and rotate the perforated pan.
However, often the coatings being used in the process can be very difficult to clean. A classic example of this is the cleaning of pigmented HPMC based coatings. Where the HPMC is itself not difficult to clean, the water or alkaline detergents strip off the polymer, leaving behind the pigment (usually iron oxides or titanium dioxides). This results in coloration or haze formation which is tough to clean and often time tough to see on the surfaces of the tablet coater because of the dark tank. An LED light may need to be used to see this haze and often requires strong corrosive acids and manual cleaning to physically scrub it off the surface of the equipment, which is not desired.
Selecting the optimal detergent for your tablet coating soil that readily removes the entire formulation in a single detergent step is often the solution for cleaning the coater pan. The detergent solution can prevent the pigment from bonding to the equipment surface and eliminating the need to re-clean.
Limited Cleaning Options for Blending Equipment
From ribbon blenders to V- blenders, these critical pieces of equipment also have unique cleaning challenges. Most of them center around the limitations of automated cleaning. The most common cleaning process for these pieces of equipment are to fill the mixing vessel with detergent solution, soak and agitate the vessel for a previously determined amount of time. Parts that can be removed, like mesh screens and blades, are often cleaned via a clean out of place procedure such as manually scrubbing. This manual action is best avoided in a GMP cleaning process as it is operator dependent and inconsistent. Also, due to safety and ergonomic issues, manual cleaning action must be minimized or eliminated in cleaning of production scale equipment.
4 Reasons Cleaning Knowledge is Essential
The main reasons that knowledge of cleaning is essential to any manufacturing company:
-
To ensure operator, environmental and equipment safety
-
Downtime reduction
-
Maximum equipment utilization (equipment longevity)
-
Savings – Resource and labor costs
Elaborating on these points, we can conclude that considering all cleaning variables above before moving cleaning to full-scale production, helps in identifying your optimal cleaning process that satisfy profit requirements of a company. This ensures that your cleaning is consistent, robust and repeatable and creates minimal resource usage and downtime while maximizing your equipment utilization.
A Complete Solution for Your Production
You are not alone when facing your cleaning challenges. Dober’s Chematic Cleaning Chemistries and custom cleaning evaluations reduce your cleaning time and eliminate the need to re-clean equipment. We pride ourselves on thinking differently about cleaning. We believe that every production facility is unique and so are the residues they create. This is the reason we develop cleaning detergents that are formulated for you and not "off-the-shelf" solutions.
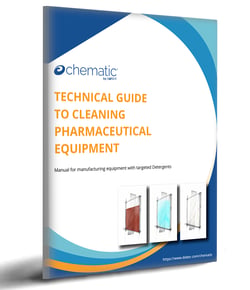
Download the full copy today.
Begin building better business efficiencies with a new understanding of the equipment cleaning process.